7 Steps To Take Before Implementing a Monitoring Solution
Seven Steps To Take Before Implementing a Monitoring Solution
While most people may consider the undertaking of changing their environmental monitoring system or adopting a new EMS altogether to be overwhelming, the implementation doesn’t have to be as daunting as one may think.
We don’t need to tell you about the need for a monitoring solution, a system designed to protect equipment and facilities from minor setbacks, catastrophic failures, and everything in between… However, many teams put off their monitoring initiative because they think it will be a much larger task than it actually is, they’re reluctant to change, or they think it will be a massive upfront capital expense.
Wondering where to begin? How long it takes, or how much it costs? Or what you’ll have to do before, during, and after implementation? You are not alone. We’re here for you, and the good news is that implementing an EMS is not something you have to do alone. There are monitoring partners that can do the heavy lifting for you and ensure everything is set up - and managed - properly.
In this article, we’re introducing a standardized approach to implementing an environmental monitoring service, sharing what to consider before implementation to ensure you will have full insight into your facility, laboratory equipment, and scientific resources.
Let’s discover the seven steps to implementing a monitoring solution in your facility, and the role your team and monitoring partner will play in the implementation process.
Step One: Define Your Drivers
Most labs don’t proactively monitor equipment or facilities. Sadly, most labs take a reactive approach: addressing problems after they’ve arrived, which, in a lab, can mean a failed experiment, loss of time, money, and often highly precious resources.
Before implementing a monitoring service, look at any/all issues driving the decision. Perhaps it’s in response to a recent outage? Or a new auditing requirement? Or a desire to move from reactive to proactive or predictive? Or a lack of insight?
Delineate the problems before designing the solution.
Step Two: Identify Your Parameters
Next, you’ll want to identify parameters specific to your business, facility, and equipment.
For example, depending on the nature of your work, a minor fluctuation in equipment temperature could be meaningless… or devastating. Some facilities require 24/7/365 service, whereas others only during working hours.
And consider what’s next, too. Markets and business needs are constantly in flux, and you’ll want to ensure flexibility in your parameters to address inevitable change. I.e., when you identify your monitoring parameters, be specific, but not restrictive.
Step Three: Qualify Vendors
With parameters and processes in hand, the next step is choosing a vendor.
Laboratory monitoring services should be custom for each lab, but ideally, your vendor will have some general, related experience. I.e., while the output of IVF facilities varies, they all typically require robust cold storage units–your vendor should have experience monitoring the type, if not the exact model, of equipment you use.
Most critically, your vendor should be able to prove FDA compliance. While this sounds like a no-brainer, more than a few labs have taken serious steps with a monitoring service provider only to find out too late that that provider lacked FDA compliance. Get documentation in hand, up-front.
Step Four: Ensure Adoption, Not Just Implementation
A laboratory monitoring solution is not a “Field of Dreams.” Just because you build it, doesn’t mean they will come and use it. Part of your plan–created with your vendor–is to ensure adoption, which means training and education as part of the deliverable. It also means communication, and lots of it.
This begins prior to implementation:
Get buy-in and input from impacted departments and people.
Address their processes and parameters.
Determine what their training needs will be.
Create a cross-department, cross-functional, in-house team to take part in the implementation (or to at least be informed at critical milestones).
Putting a monitoring solution in place and ensuring it’s used effectively requires collaboration and communication.
Step Five: Integration
When you say “integration,” people typically think of “systems,” which is absolutely true. Your service provider should have the capability to integrate the data flowing from your monitoring solution into larger business systems (such as a LIMS, an ERP solution, or a BMS). You’ll want an open API.
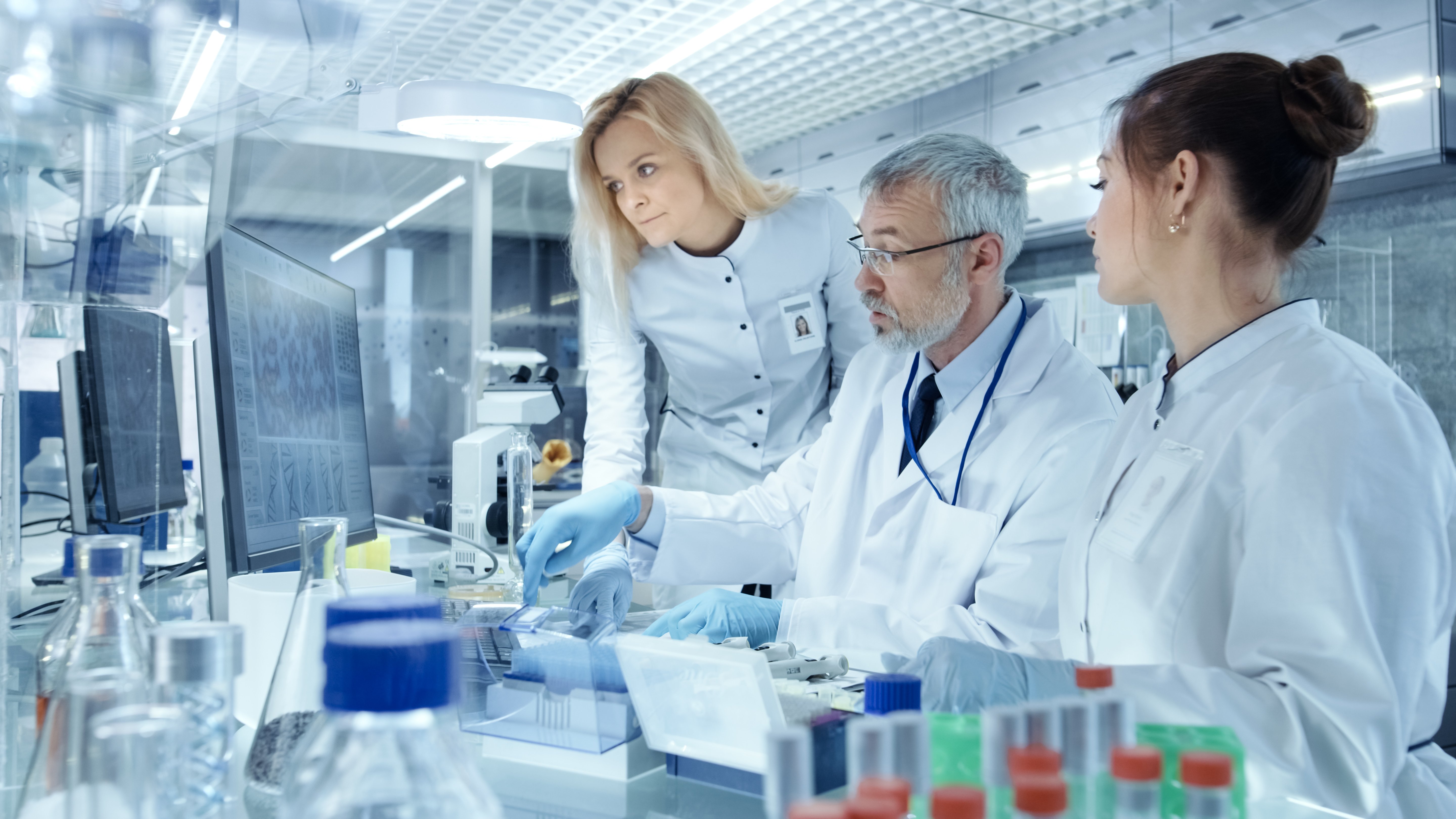
However, with a lab monitoring service, there is also hardware integration to consider: the probes and sensors that collect the data. You must ensure that data is “packaged” and easily captured by your monitoring system and then quickly disseminated throughout your organization and its connected systems.
Another integration factor is workflows. A laboratory monitoring system should, for the most part, integrate with existing workflows and processes. The implementation should not overly disrupt ongoing work, nor should its everyday use post-implementation. Remember: services like these exist to serve the business, not the other way around.
Step Six: A Data Plan
No, we’re not talking about mobile devices; we’re talking about what you will do with the data your monitoring service collects. How will you share it? With whom? How will it be acted on? Will it be enough for, say, an audit trail?
Before the deluge of data begins post-implementation, a plan should be in place. Your implementation partner can and should help you build this plan, and this is where you need to assess the bona fides of that partner carefully. Ask to see data outputs and techniques from other clients, and ensure your provider has both the systems and industry expertise to help you build an actionable data plan.
Collecting data is one thing, but acting on it is the main thing.
Step Seven: Future-Proofing
Finally, ensure your implementation is as future-proof as possible.
Change is a constant in the lab, and being able to adapt/scale is essential. Outside the lab, change is also a constant: new regulations, environmental conditions, and business requirements. A monitoring system must be capable of pivoting when necessary.
This is why monitoring-as-a-service is typically the best choice for a lab.
It requires no investment in hardware (the least scalable thing any business can ever buy), no investment in infrastructure (which often involves updating), and, should personnel changes occur within your company, your laboratory monitoring service won’t change. (People often “take their expertise with them” when they exit.)
We hope you’ve found this outline helpful. We're here to explain anything further and help you take some next steps in implementing a scalable, data-rich/data-driven, future-proof laboratory monitoring system. Contact us now.